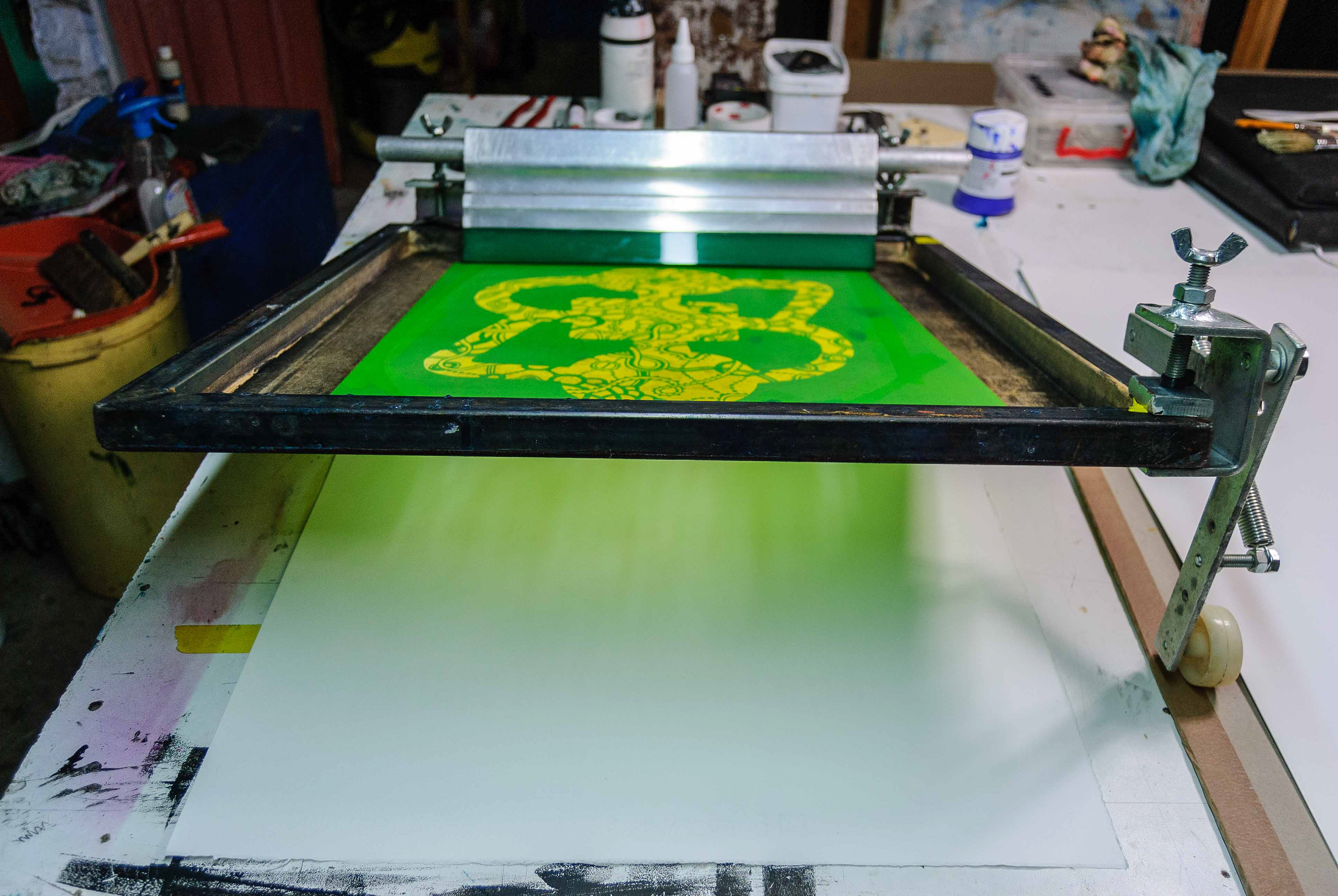
Starting to print an edition
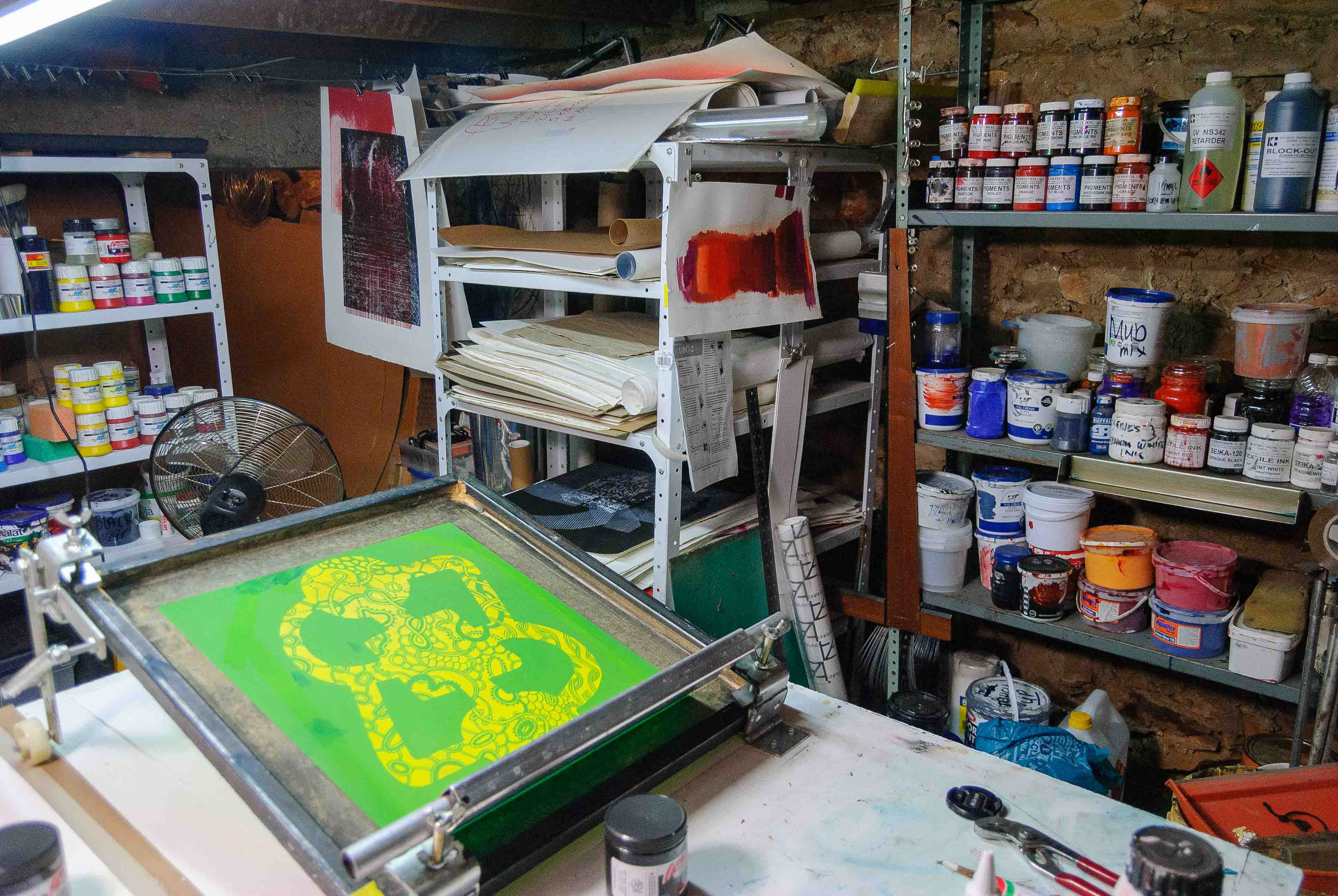
A general view of the print studio
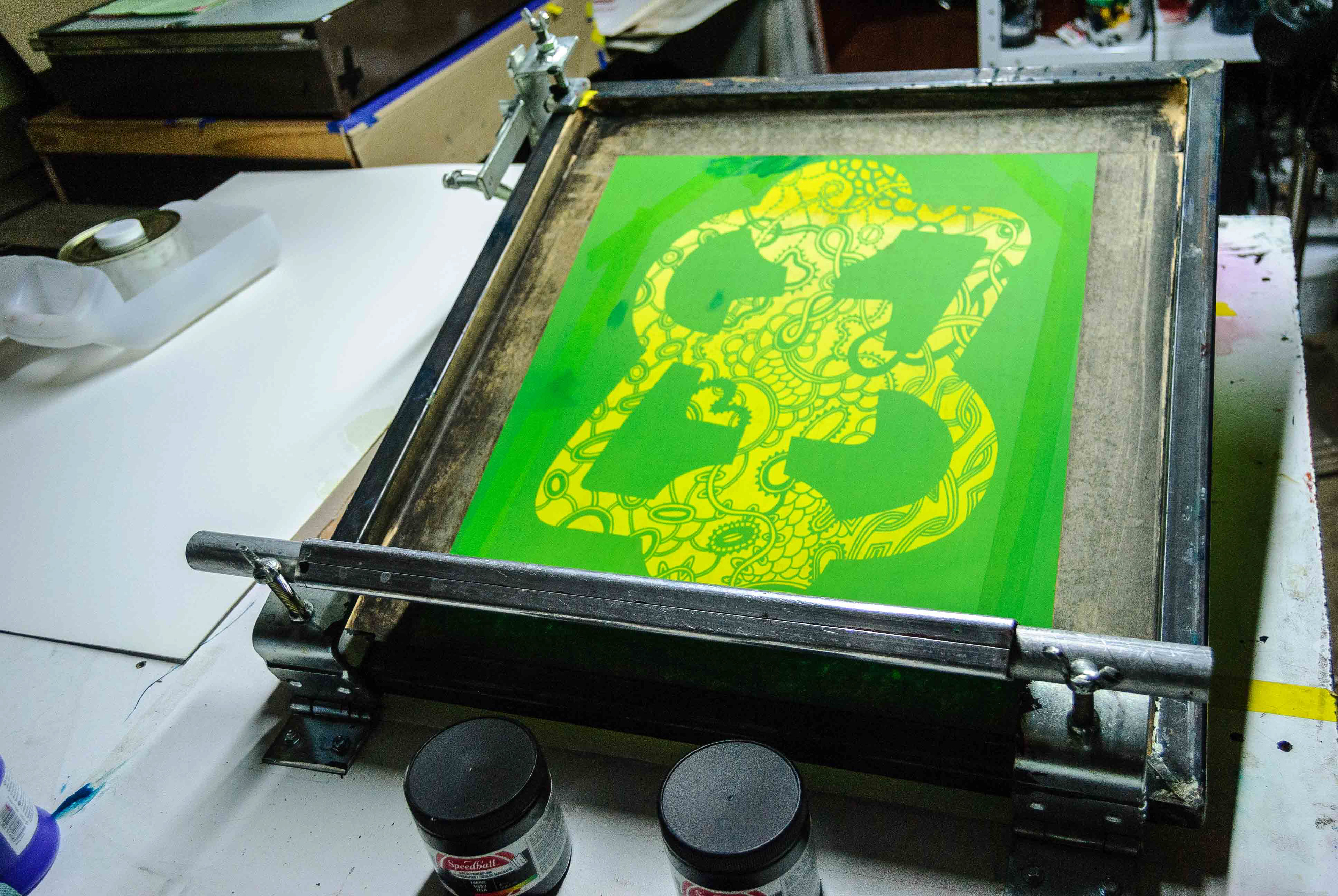
Another view of the silkscreen in use
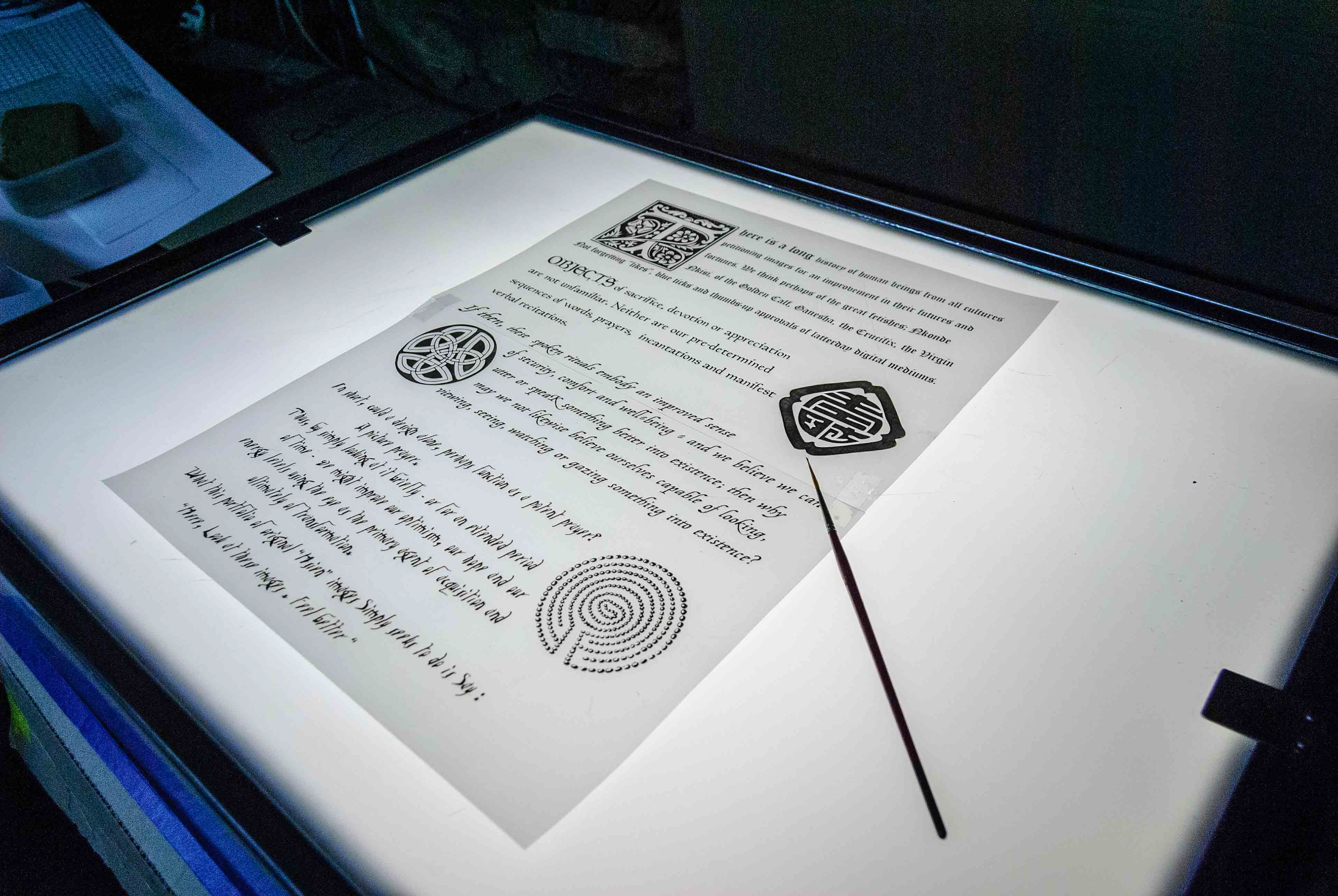
A silkscreen positive being examined and retouched where necessary
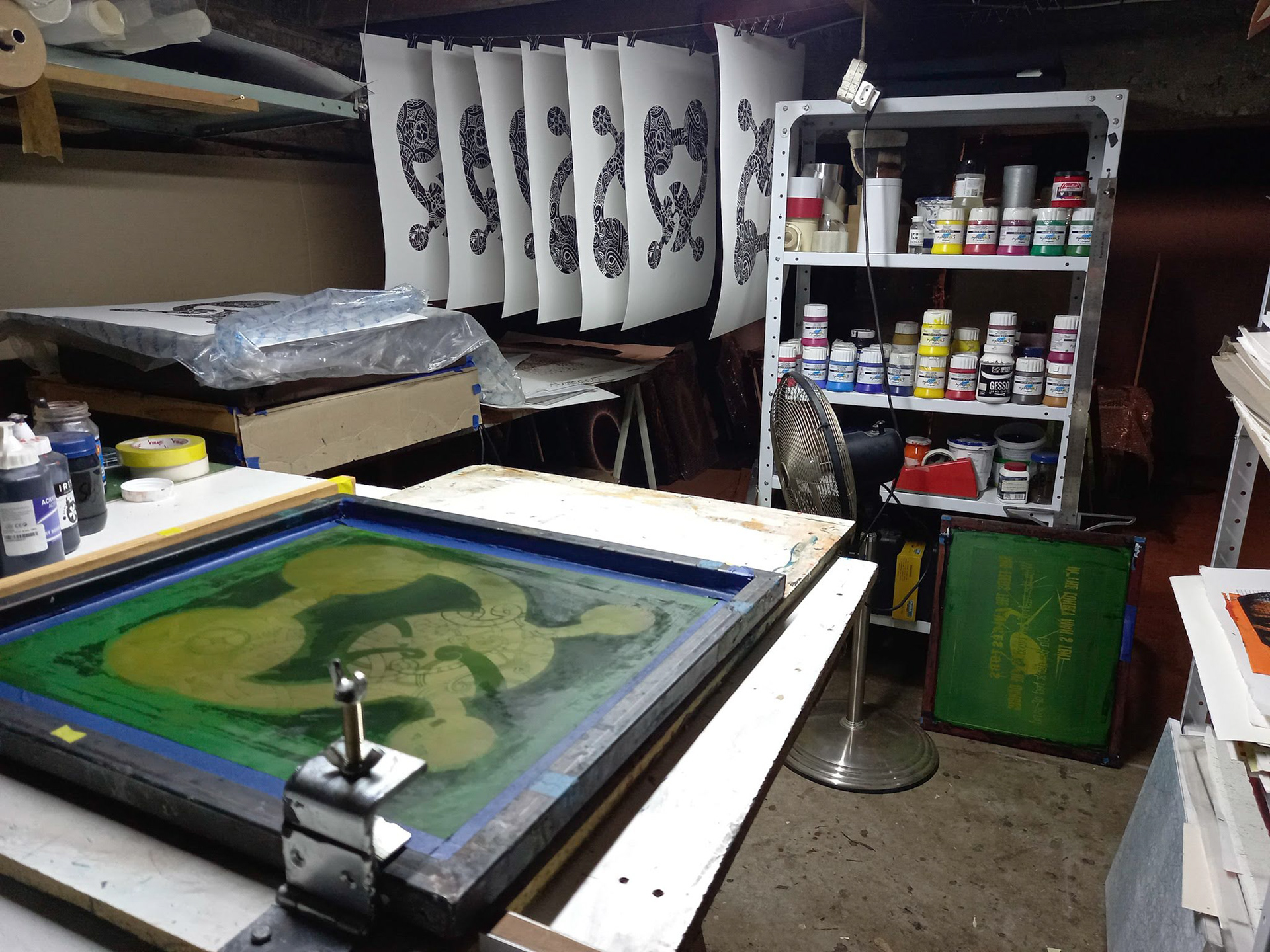
End of an print edition
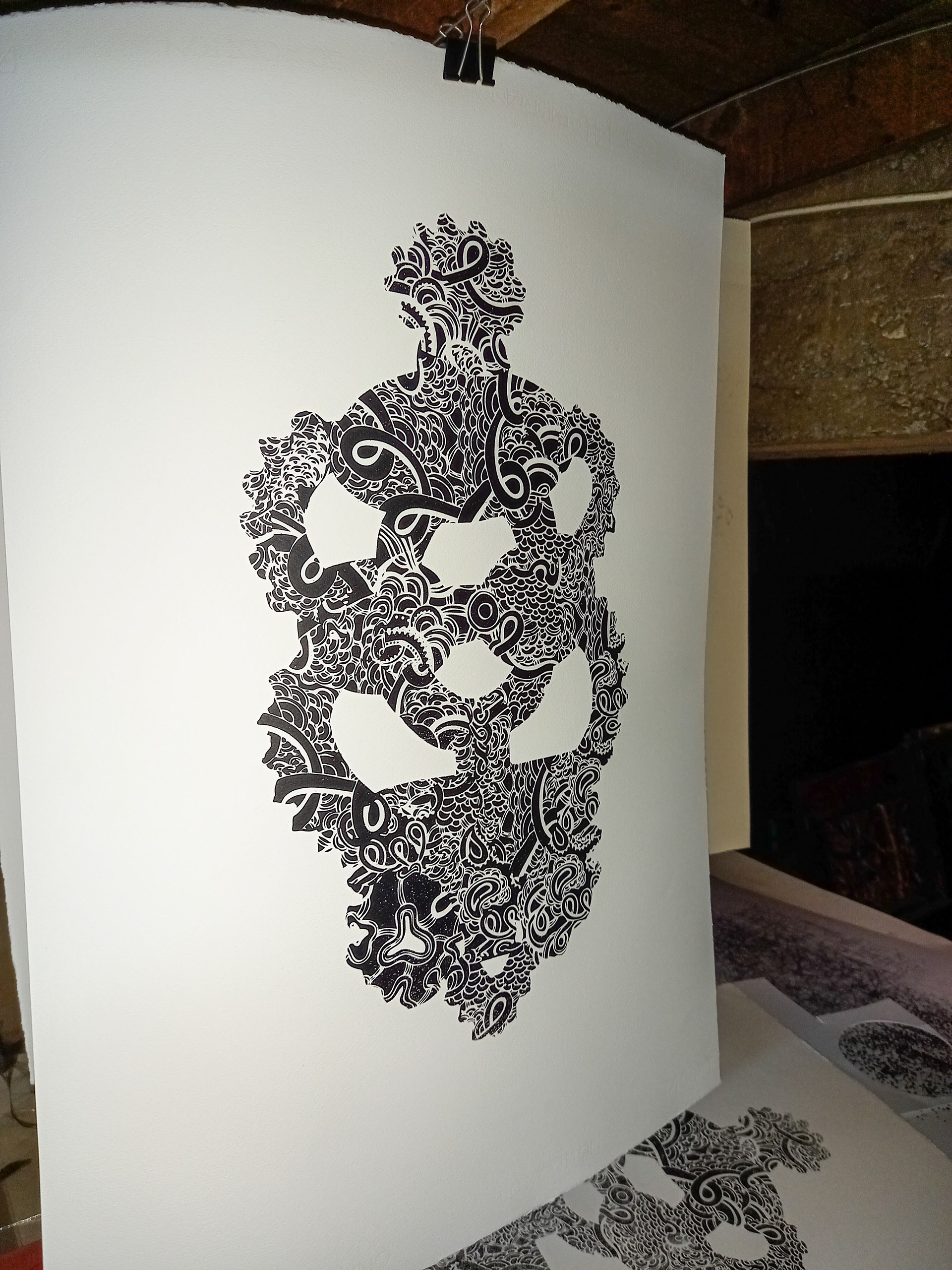
A print hanging out to dry
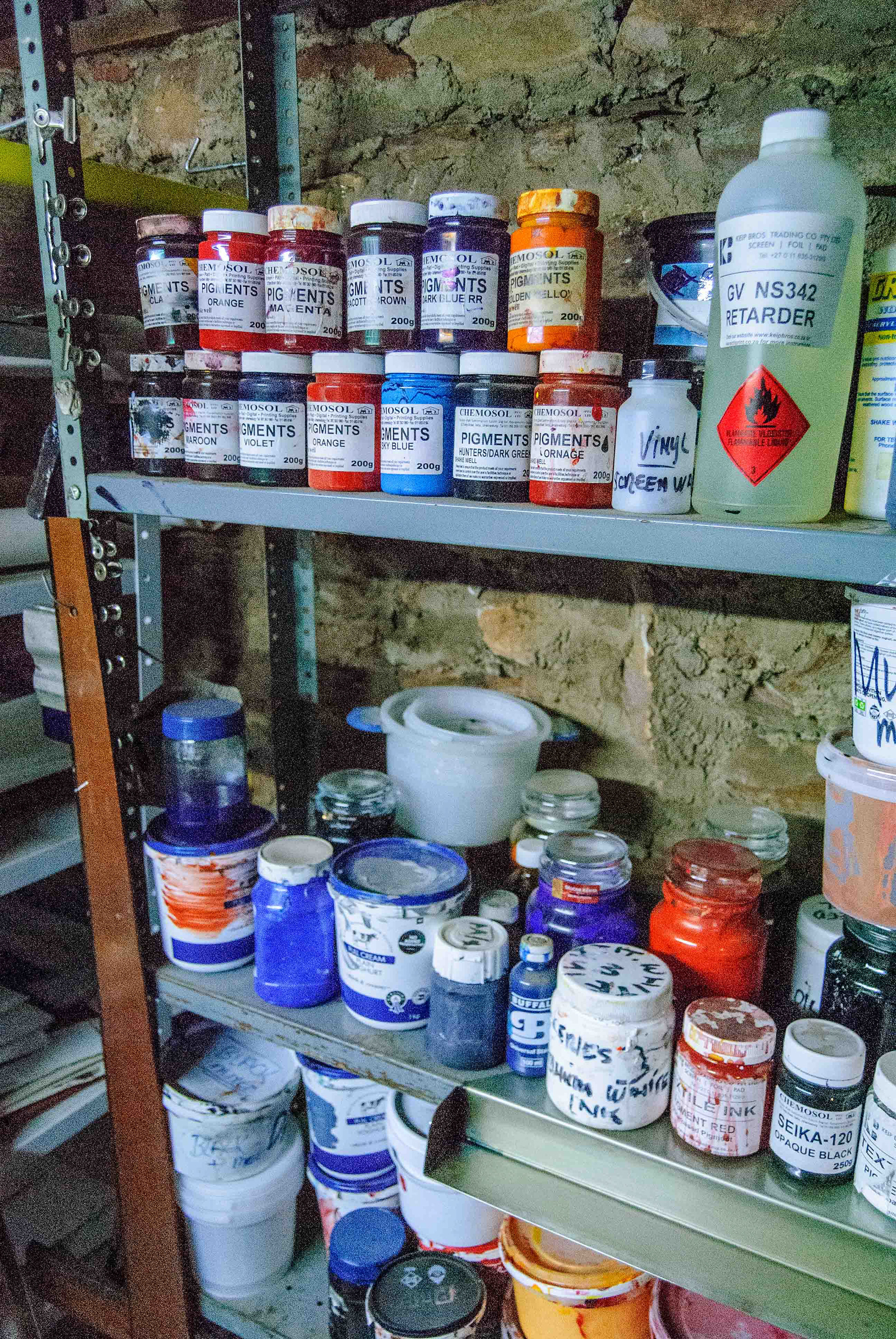
Various ink pigments and silkscreen solvents
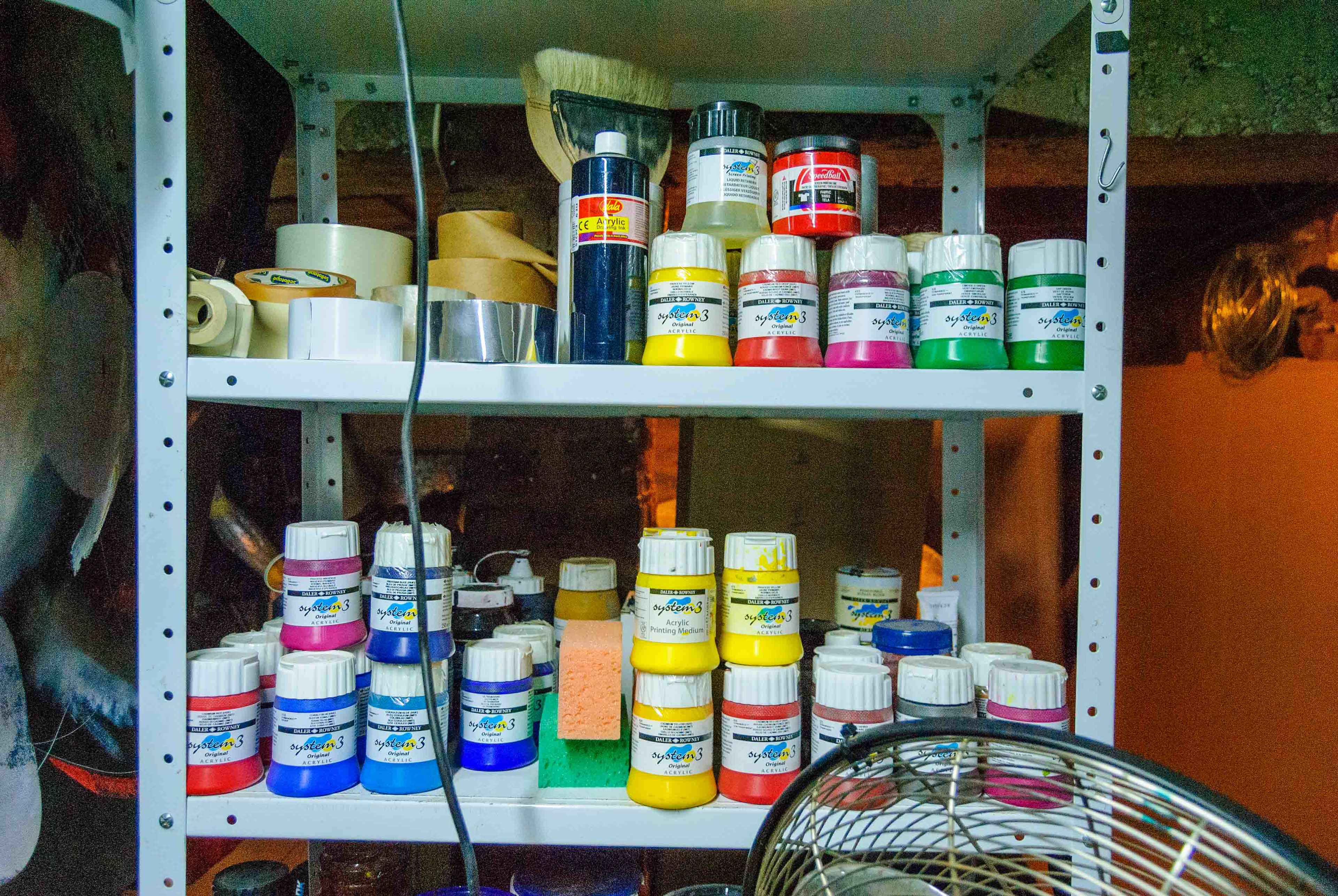
Rowney System 3 Acrylics and mediums for painting and screenprinting
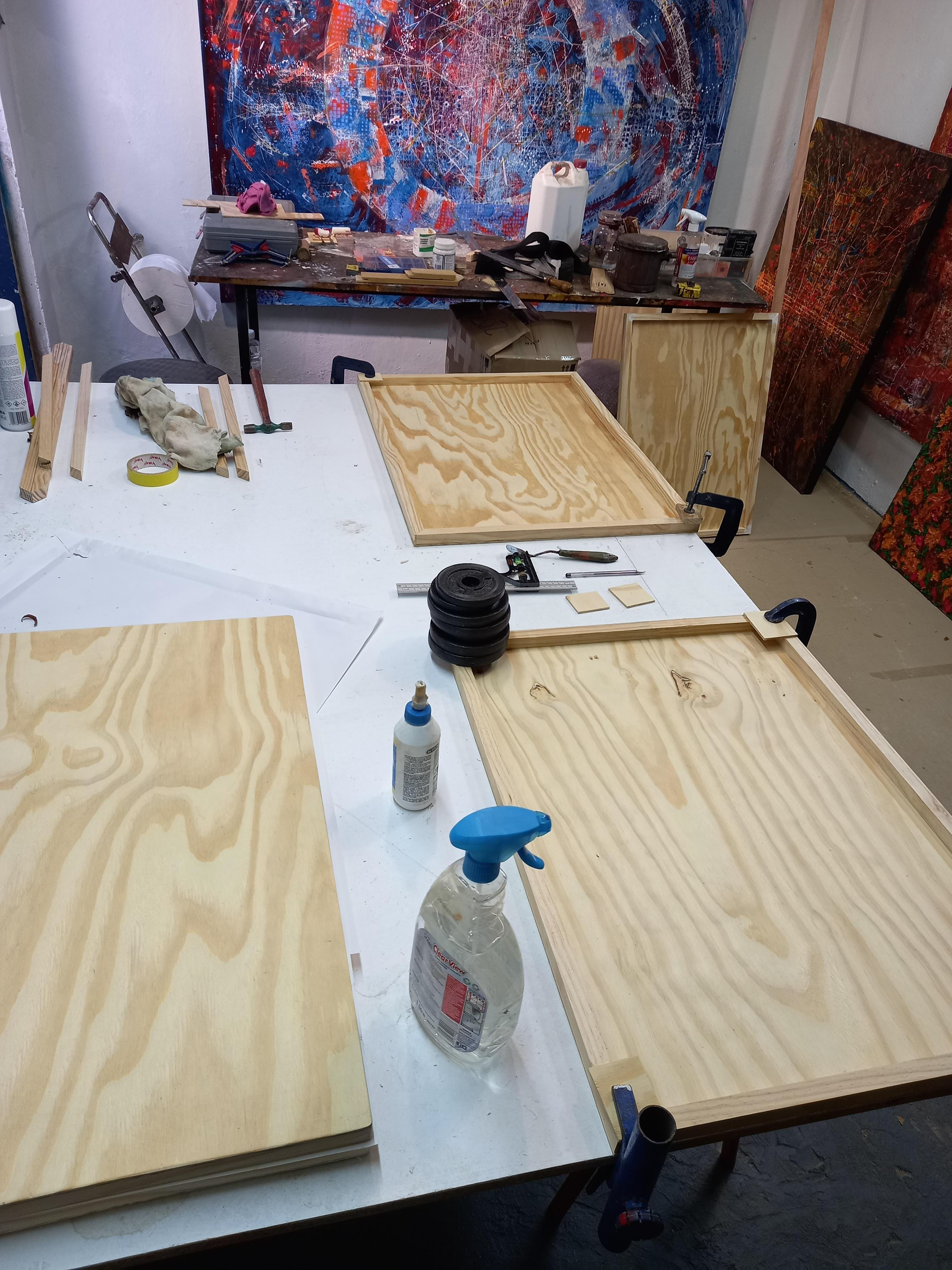
Making the portfolio boxes
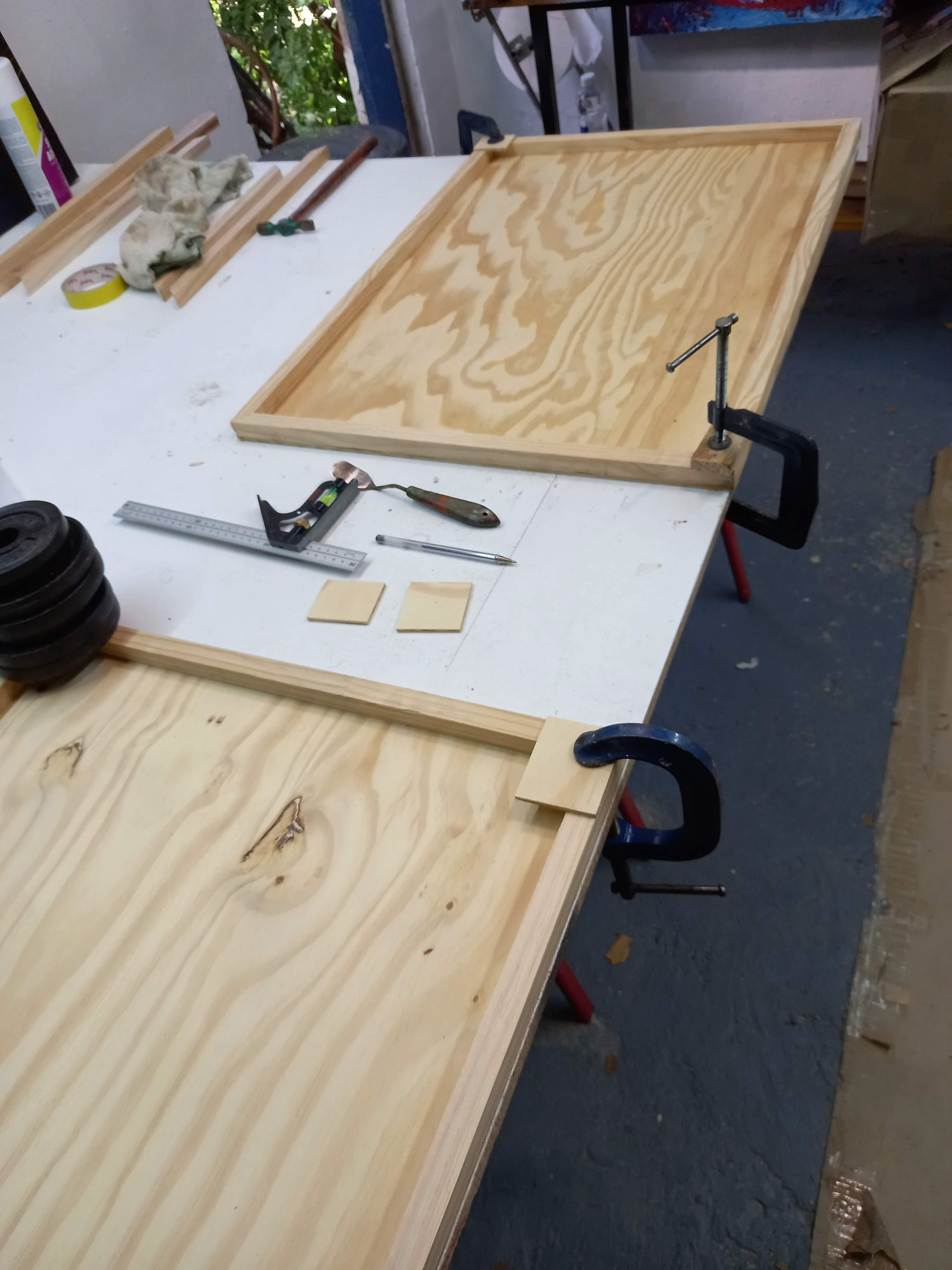
Making the portfolio boxes
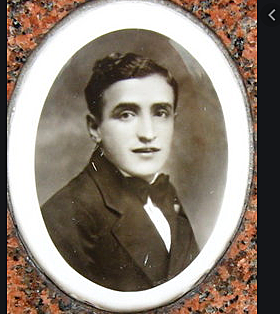
In 1907, Samuel Simon of England was awarded a patent for using silk fabric as a printing screen.
A description of the silkscreen process used in
making the Hsien Prayer Prints
making the Hsien Prayer Prints
The silkscreen process, also known as screen printing or serigraphy, is a versatile printing technique used to transfer ink onto various materials such as fabric, paper, metal, glass, and plastic. It involves creating a stencil, known as a screen, which allows ink to pass through onto the desired substrate in specific areas.
1. Design Creation: A design or artwork is created digitally or by hand, keeping in mind the desired image or pattern to be printed. The Hsien artworks were originally created by hand by Nicholas P. Hauser and then digitised in order to make silkscreen positives.
2. Screen Preparation: A fine mesh screen, traditionally made of silk (hence the name), but now usually made of synthetic materials like polyester, is stretched tightly over a frame. The screen is then coated with a light-sensitive emulsion.
3. Stencil Formation: The designed image is transferred onto the screen using a photographic process. The screen is covered with a film positive, which is a transparent film with the design in opaque ink or toner. It is exposed to light, and the emulsion hardens in areas not blocked by the design.
4. Washing and Drying: After exposure, the screen is washed with water. The areas where the emulsion was exposed to light dissolve, creating stencil openings that correspond to the desired design. The screen is then dried.
5. Ink Preparation: The desired ink colors are prepared and mixed according to the design requirements. The ink used in silkscreen printing is typically thicker than other printing methods to prevent excessive spreading.
In this Hsien project, Speedball Black acrylic textile ink was chosen because of it's qualities of permanence and pigment density.
6. Printing Process: The prepared screen is placed on top of the substrate to be printed. Ink is poured onto the screen and spread across it. A squeegee or a rubber blade is used to push the ink through the stencil openings and onto the substrate, while ensuring even pressure and coverage.
7. Multiple Layers and Colors: For multi-colored designs, the process is repeated using different screens and corresponding inks. Each layer is aligned precisely to ensure accurate registration of the colors.
For this project's current series edition we only used black ink, but future series of editions may well include a second colour or more.
8. Curing or Drying: Once the printing is complete, the ink on the substrate needs to be dried or cured. This can be done by air-drying, heat curing, or using ultraviolet (UV) light, depending on the type of ink used. In this case, air-drying was used..
The silkscreen process is popular for its ability to produce vibrant and durable prints on a wide range of materials. It is widely used in various industries, including textiles, signage, promotional products, and fine art printing.
The History of Silkscreen Printing
Screen printing, screenprinting, silkscreen printing, serigraphy are ways to identify an essential simple process with a long history in both art and industry.
Along with its variety of names screen-printing is also a history of complexity in intent, technique and artistic use. As a stencil process that blocks areas so another allows ink to pass through, screen printing is generally credited to China during the Song Dynasty (960-1279 CE). Other Asian countries, such as Japan, would further add innovation in combination with block printing and hand applied paints.
One advantage is that screen printing does not need a press, as in etching, inks can be adjusted for multiple surfaces from paper to ceramics and the application surface does not need to remain flat. Silkscreen printing refers to the original mesh used with a stencil; nylon, polyester and metal can replace the screen for the applied stencil. Whatever the choice of screen, it is most often affixed to a metal or wooden frame.
The Englishman Samuel Simon patented the screen printed form most familiar in the Western world in 1907. While Europe was introduced to the process in the 18th century, it would take the affordability of silk mesh and commercial use of the process to make it more available.
Simon’s use of his patented process was primarily used for printing expensive wall coverings on silk, linen, paper and other fine fabrics. Early in 1910, along with photography, screen printers began experimenting with photo reactive chemical processes. Roy Beck, Charles Peters and Edward Owen are credited with the beginnings of a myriad of sensitizing processes still being refined by artists and industry.
A group that formed the National Serigraphic Society first used “serigraphy” as a term to describe fine art created with this technique. This shift served to legitimize this technique in its two separate applications. The term came from the Latin “sericum” (silk) and the Greek “graphien” (draw or write). This distinction would lead to the development of the prominence known in the United States of “Pop Art” and the artist Andy Warhol.
(Credit: History of screen printing, Catherine Sullivan, Curator JTPM)
(Credit: History of screen printing, Catherine Sullivan, Curator JTPM)